How to Maintain the Depth Rating of your Trench Shields?
- ESC Group
- Oct 9, 2024
- 8 min read
Trench shield or trench box equipment, whether owned or rented, must undergo regular inspection and maintenance to ensure their strength and functionality. Trench shields - steel and aluminum, are inherently durable and long-lasting but this also depends on how it is manufactured, used, handled, and maintained.
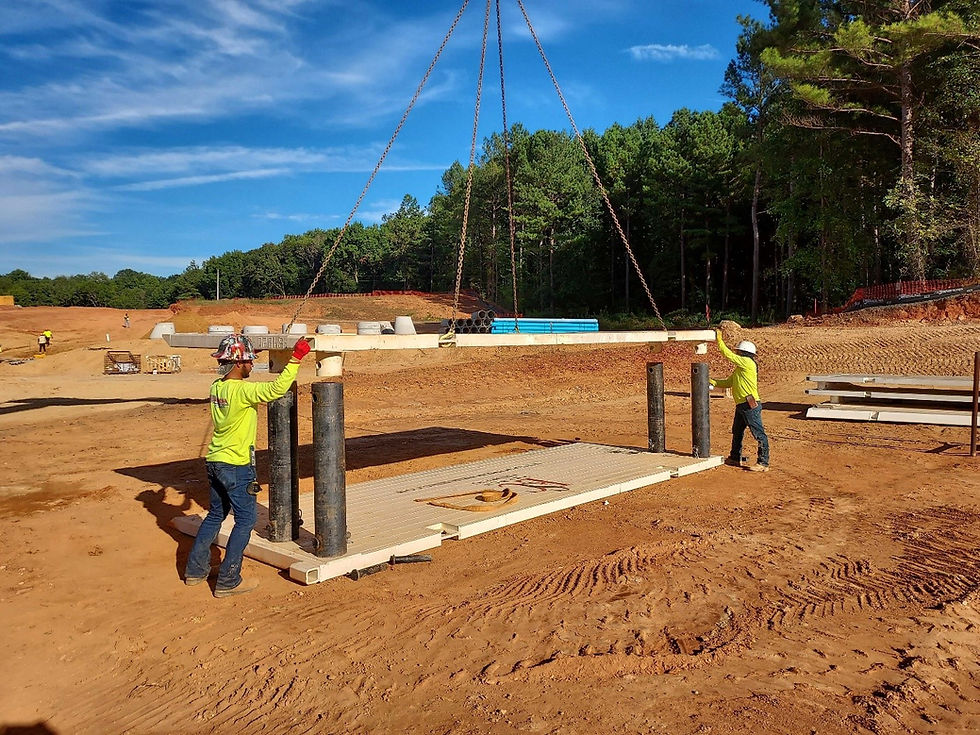
When put to work, trench shields encounter outside forces that squeezes and possibly bends the shields or panels. If the yield strength is not exceeded, it will return to its original condition and retain its original strength. If the yield strength is exceeded, deformation of panels and other parts can occur at the least, or; the whole shield system fails as a worst case scenario. In case of failure, here comes the tricky question – should the owner retire the equipment or repair the damages at all costs?
What Industry-experts Say About Shield Inspection and Repair
Sizing and selection of a trench shield for a particular excavation or trench work requires identifying the soil type, depth of cut, size of utilities, and equipment capacity, as a minimum. With this set of information, shortlisting of options is done by referring to a depth rating matrix also known as the manufacturer’s tabulated data sheet. The selection is then narrowed down to the most conforming model according to the criteria correlated and as recommended by a Registered Professional Engineer (RPE).

Over a year ago, North American Excavation Shoring Association (NAXSA) published insightful literature about waffling effects and other prevalent damages on trench shield components. Though some wear and tear is expected, other types of damage can be highly detrimental and possibly cause panel failures as featured in the article. Providers and users are reminded to be extra vigilant in evaluating the integrity of trench shields or trench boxes before deploying them onto sites.
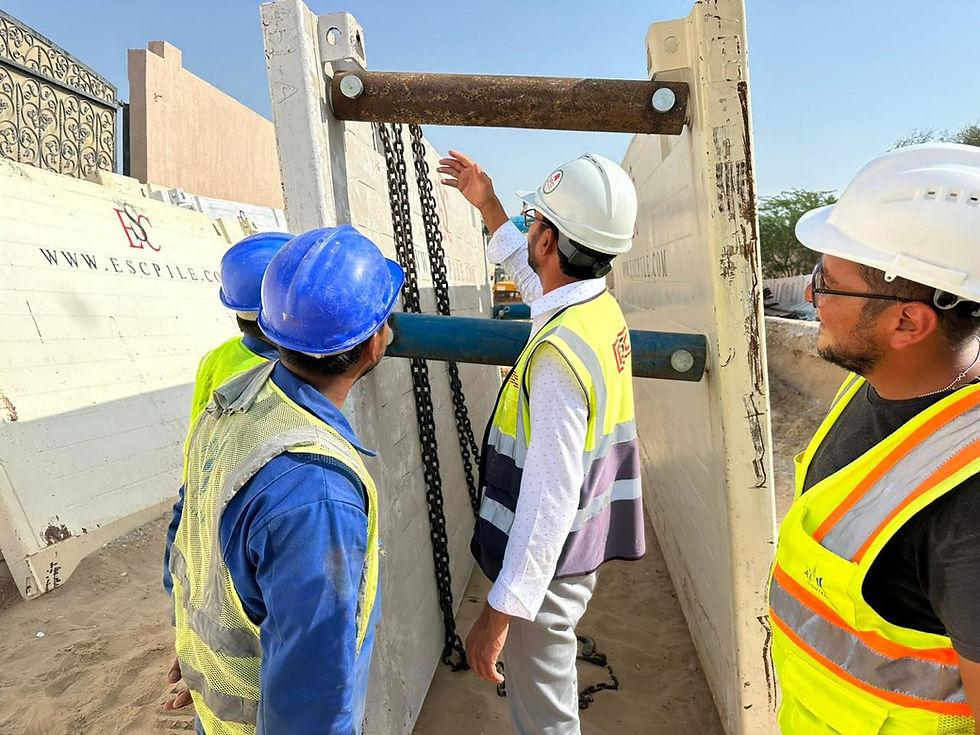
NAXSA also brought up the downgrading of the performance rating of a damaged trench shield to suit applications involving lower soil pressures. Its adequacy or estimated strength, of course, can only be confirmed by an RPE or ‘Competent Person’ as identified by OSHA. The industry has varying takes on how to deal with shields in less-than-ideal conditions. Besides removal, downrating is considered a practical option when damages show evidence of exceeded yield strength and when repair is difficult. From a general perspective, repairing trench shields to restore their original state still appears as the best resolution for all types and cases of deterioration.
Understanding the Behavior of Shields in Details
While OSHA-provided information regarding inspection and maintenance is generic, industry experts made it easier for the public to create effective inspection and maintenance checklists for shielding equipment. The system enables thorough inspection of structural elements by the concept of mapping, giving hints on specific areas to look at and translating the meaning and weight of each damage observed. Looking into the structural parts:
Shield Wall/ Shield Panel: Applying structural analysis theory, a trench panel or panel box is modelled as a beam of varying width and length that is supported at the ends only. Upon application of lateral load, it will bend in the middle. The middle third or simply the middle section of the wall is the critical area. This area should have no punctures, dents, or waffling (skin plate pushed-in around the ribs). According to NAXSA, the skin plate is a very important element of the shield’s structural strength. When a shield panel is put under load, both inner and outer skin plate is subjected to tension. If the skin plate is stretched repeatedly, it will not be able to perform as intended, and the shield’s strength is reduced. In figures, the maximum allowable deflection of a simply-supported panel is the quotient of length (L) divided by 150 or L/150. Normally, it should not go over 2 inches to avoid permanent damage. Once the panel reaches its yield strength, it develops a permanent bend that stays even after retrieval. The panel may be straightened back by imposing pressure from the opposite direction but its structural capacity is no longer the same.
Panel deflection is the best indication to know whether the shield is within the allowable load range or about to give-in. As a factor of safety, deflections should be watched closely and kept within a comfortable range, say 80% of allowable. Minor dents, punctures, or cuts found outside the middle third of the panel generally have a minimal impact on its strength and can wait for completion to undergo repair. Otherwise, damages inside the middle section or any extent of warping or waffling at any point of the panel must be given immediate attention.

End Channel or End Post/ Column: Ideal trench shield stress loading is similar to that of a cantilever column. Pressure is largest at the bottom and decreases as it goes to the top. When panels are pushed by soil from outside, pressure is transferred to the end channels, then carried to the struts. End channels or end posts are heavily-reinforced elements that encloses the shield panel vertically at both ends, and where spreaders are connected in majority of manufacturing cases.
When resisting lateral forces, the lower portion of the shield and eventually end channels, is pushed inwards, while the upper portion is pulled towards the outside. The two panels are held together by two layers of heavy-duty strut or spreader at both ends, with the lower layer located slightly over the middle height of the shield. Simulating this arrangement, maximum pressure is expected to take place at the collar of lower spreaders, that is exactly underneath of the lower spreader adaptor. Trench shield failure is mostly a result of bent end channels being pushed to limits or exceeded yield strength. End channels or posts are inspected for bending. Users and vendors should always look carefully under the lower collar for signs of overstress such as a wrinkle, crease, or dents.

Spreader Adaptor/ Spreader Receiver: Collars/Receivers are inspected for roundness, corrosion, and cracks. Spreaders must be properly fit and intact against the collars/receivers to ensure interconnectivity and efficient transfer of loads. Oval-shaped collars/receivers create eccentricity that can cause huge movement of the shield wall and possibly trigger rotating of the toe. The upper collar/receiver acting in tension is generally the more critical member than the lower receiver in compression. This is because steel as a material has better compression strength than tension strength.
Spreaders/ Struts: Spreaders are available in fixed and adjustable or telescopic type. Adjustable spreaders are intended for necessary on-the-spot adjustments to achieve the best fit of trench shield against trench walls. Although steel is stronger in compression, lower spreaders as compression elements are heavily-strained specially under extreme loading conditions. On the other hand, upper spreaders in tension are tremendously stretched, creating high stresses on the locking pin and holes. Due to these factors, spreaders are always fabricated from Schedule 80 pipe materials and preferably extruded.
Lower spreaders are checked for buckling, roundness, and dents. The pipe must be perfectly round at any section of its length. Oval, buckled, and dented pipe losses its strength when compressed and ultimately fold or bend. Slotted holes and cracks at the upper spreaders are dangerous and needs immediate action. Elongated hole is an indication that the pipe is already stressed beyond limits.
Push Pads or Top Beams: Push pads or crush beams are inspected for punctures, cracks, and excessive dents or deformation as a result of frequent pounding specially in knife-edge panels. When the top beam has weakened or severed at its middle third section, its overall integrity is already compromised and must not be used until repaired. Pounding caps are used to avoid this issue. In any circumstance, a damaged panel should not be used in deeper segments of a trench. They can be stacked as top walls only when a competent person says so.
Locking Pins and Keepers: The correct material grades, dimensions, and shapes must be used. The use of alternative locking materials to replace missing pins is not allowed. Pin keepers should be always in place.
Important Figures in Shield Inspection
The ‘competent person’ can use below data as quick reference to identify the severity of damages in trench shields. However, this reference is general in nature and may not necessarily apply in all cases. The health state or condition of a trench shield unit is still within the prerogative of a PRE to specify.
Shield Wall Horizontal Deformation Limits:
Length ≤ 12ft: ½ inch max.
Length 12ft ~ 20ft: 1 1/4 inch max.
Length ≥ 20ft: 2 inches max.
Shield Wall Vertical Deformation Limits:
Shield w/ pipe clearance > 72 inches: 1 inch max.
Shield w/ pipe clearance < 72 inches: ¾ inch max.
Collar Pin Hole Deformation Limit: ½ inch max.
Flange Curling Deformation Limit: 0.0625 X nominal shield wall thickness
From ESC’s Perspective
For safety, companies should always implement a zero-risk policy and call for the removal of damaged shields immediately from job sites. Another reason behind this scenario is the absence of resources to deal with repairs such as manpower or plant & equipment. Companies with appropriate resources in assessing and reconditioning damaged shields has two viable options: downgrade the shield equipment to a lower but safe performance rating or; carry out repair to restore the original strength of the damaged shield unit. Again, restoration works can only be performed by certified welders, guided all the way by a ‘competent person’.
In reality, old shield equipment can still be seen in many project sites and this is not totally wrong as long as they are regularly and properly maintained and re-certified by an RPE. Contractors who have their own shields should do repair works in consultation with an RPE who can later issue re-certification of tabulated data. Contractors may also send damaged shields to qualified repair companies and get it re-certified by an authorized third party.
If a contractor or user prefers to rent shields, the presence of a ‘competent person’ to oversee project implementation is a must. Another way to ensure safety is to acquire the services of the equipment provider as a package deal with trench shield equipment. Users should make sure to receive rented shields in perfect condition. Whether renting new or used units, PRE stamp must be in order as a guarantee to the depth rating marking.
How Does ESC Tackles Depth Rating Related Issues?

Basically, ESC aluminum and steel trench shields are designed to cater to the unique requirements of the United States and North American construction practices, and are certified by a third-party Engineer in the USA. ESC is a manufacturer and provider of quality and comprehensive trench solutions not only in the USA but globally. We design, build, innovate, and our commitment to the industry does not end in just manufacturing high-quality trench solutions but by creating advanced and sustainable options that minimizes risks and extends money value. ESC trench box series is equipped with brief but significant improvements that helps to address prevailing problems in trench shield applications.
Our TSB Series offers a innovated hollow section/tubular design. This design, because of the lack of an internal structure will not have the waffling problems the plate and frame style boxes are susceptible to.
Optional fifth lower spreader to counter over-turning of toe and to lessen pressure at the collar neck of lower spreader. Majority of trench shield failures are caused by bending of end beam and panel below the spreader collar. Employing a fifth spreader helps prevent this occurrence.
¾ inch thick standard push pads to prevent top beam damage.
Heavily-reinforced end channel for efficient load transfer and counter buckling or bending at middle height.
Heavy duty, thick wall spreaders built via through-wall connection. This type of spreader connection is more effective in transferring load to the panel. Connections that utilize plates to mount spreader adaptor are prone to punching that cause tearing at the shield walls.
Knife-edged base shields to anchor the base panel at the ground where soil pressure is maximum.
Panels are fully welded for maximum strength, no stitch welds or spot welds used.
ESC trench boxes which employ robust cellular design are proven to be reliable workhorses and recognized by well-known companies and organizations. As a NAXSA member, we adhere to all industry norms and regulations. Principal and other features of ESC trench boxes are as follows:
Designed and manufactured in accordance with OSHA requirements
All products are duly certified by Third Party.
Heavy-duty, robust design.
Has flexible options for fixed or adjustable spreaders.
Available in custom boxes.
Follows NAXSA – Approved shoring shield tabulated data sheet.
Can be equipped with lifting lugs.
Four-point through-panel lifting system

As a trench solutions pioneer, we draw satisfaction not only from selling high volumes of trench shield equipment and services, but from seeing ESC shield units all around the world saving lives, lasting beyond estimated strength and length of life.
ESC extends assistance for all kinds of excavation and trench projects, large-scale or small. Please explore our portfolio at www.esctrenchshoring.com and let us know where and how to help you.
Call us today at USA: +1 (980) 689 4389 & CANADA: +1 (902) 442 0800 or email us info@esctrenchshoring.com visit www.esctrenchshoring.com for more information.